Il Punto di Riordino
Il Punto di Riordino, o Riorder Point (ROP), è il momento in cui un’azienda deve necessariamente procedere con nuovi ordini ai fornitori e, dunque, provvedere al riapprovvigionamento.
Esso consente di gestire l’adeguata quantità di scorte affinché si riesca a coprire la domanda del cliente e la domanda di produzione interna nell’arco di tempo necessario al rifornimento; se correttamente calcolato, il punto di riordino evita il blocco del flusso produttivo e, di conseguenza, il flusso di evasione ordini.
Per definire e calcolare il punto di riordino è importante tenere presenti la domanda che l’azienda riceve, le tempistiche di consegna e rifornimento da parte dei fornitori (Lead Time) e il livello di scorte di sicurezza necessario ad evitare il tutto esaurito.
Occorre precisare che ognuna di queste componenti può subire importanti variazioni, dipendenti a loro volta dalla tipologia di azienda e dal tipo e dal numero di fornitori di ognuna di esse: la domanda può variare nel tempo come nei diversi periodi dell’anno o diversamente, per alcune aziende, essere costante, mentre il Lead Time dipende dal tipo di merce, dal tipo di azienda fornitrice e dai suoi ritmi produttivi e di consegna.
In funzione della variabilità dei primi due aspetti, ovviamente, varia anche il livello di scorte di sicurezza di cui ogni azienda si dota e, pertanto, il punto di riordino può essere identificato con la seguente formula:
Punto di Riordino (ROP) = scorte di sicurezza + (consumo medio, o domanda, * tempo consegna dei fornitori, o Lead Time).
Un esempio: poniamo che un’azienda soddisfi una domanda media giornaliera di 300 unità, che il Lead Time del fornitore sia di 4 giorni e che il livello delle scorte di sicurezza sia di 50 unità. In questo caso il punto di riordino da calcolare sarà:
Punto di Riordino = 50 + (300 x 4) = 1250 unità.
Quando in magazzino le scorte sono pari a 1250 unità, è il momento di effettuare un altro ordine al fornitore.
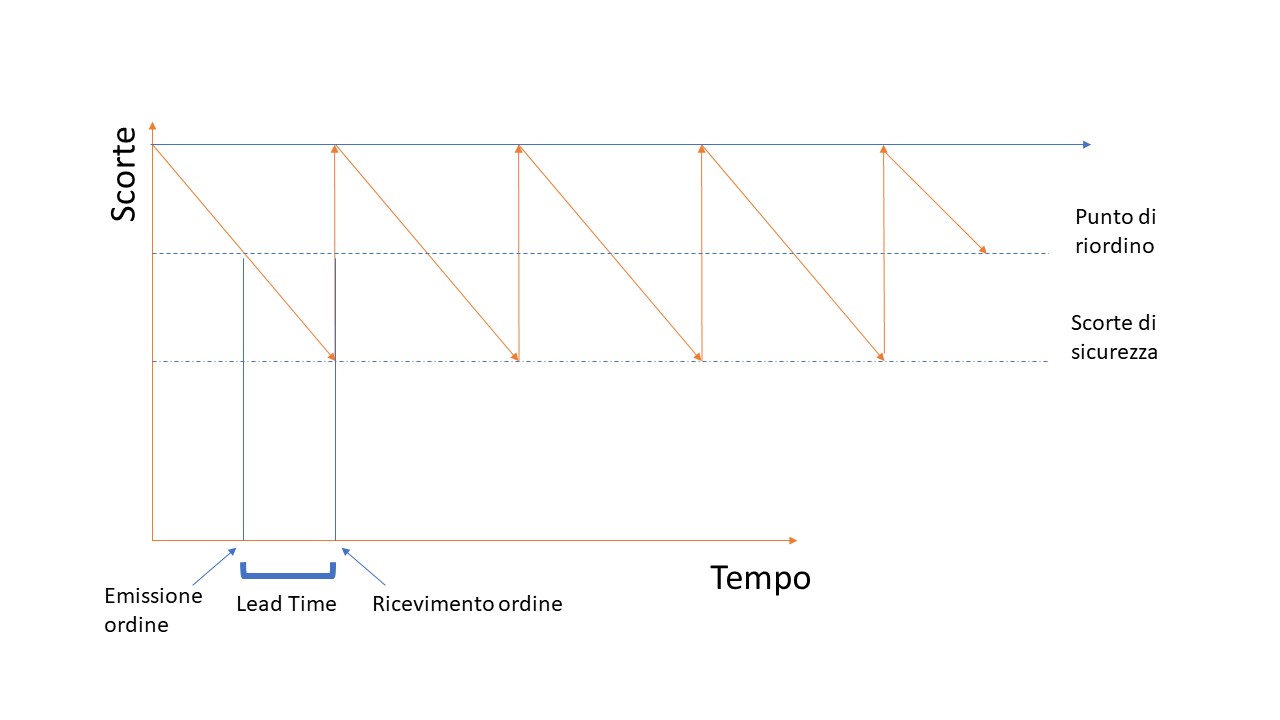
Ottenere dati il più possibile precisi, che forniscano il punto di riordino esatto, aiuta a trovare l’equilibrio tra i costi di gestione delle scorte e la capacità di stoccaggio del magazzino, quindi, ad esempio, ad evitare il rischio di una quantità eccessiva di merce da gestire sia a livello logistico che economico.
Una volta raggiunto il punto di riordino, parte la fase di rifornimento per la quale è necessaria una gestione il più possibile accurata dei dati di magazzino e delle varie operazioni logistiche. Validi aiuti sono, ovviamente, software e supporti informatici che automatizzano, calcolano ed elaborano gli uni e le altre.
In questo senso è importantissimo un ERP, sistema gestionale che pone in relazione, a livello informatico, tutte le informazioni aziendali. Altrettanto utile può essere un WMS (Warehouse Management System) che aiuta nella gestione delle attività di ricezione, stoccaggio, prelievo e spedizione, quindi in tutte quelle operazioni logistiche alla base dell’attività di magazzino.